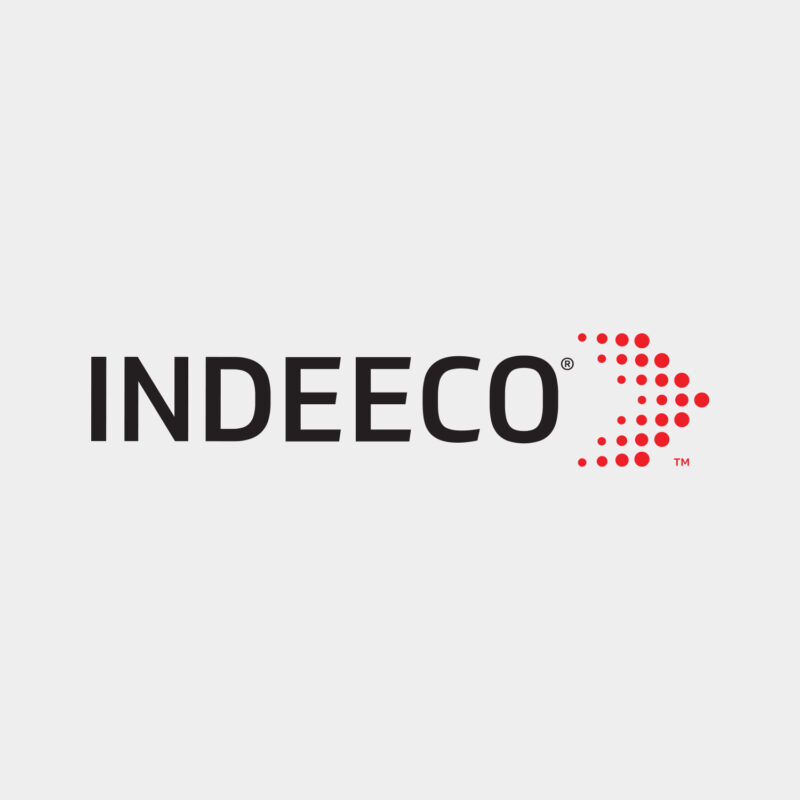
Impedance Pipe Heating Systems
Indeeco Impedance Pipe Heating Systems offer a unique, safe, and proven method for electric pipeline tracing and heating. By applying a low AC voltage through a custom-designed transformer, the pipeline itself becomes the heating element—eliminating the need for external heat sources. Indeeco provides complete, single-source support, including system design, hardware, and start-up assistance.
Ideal for heating gases or fluids, these systems are used across a wide range of temperatures to prevent freezing, maintain the fluidity of viscous materials, safely heat temperature-sensitive substances, or maintain gas temperatures up to 1600°F.
When and Why to Use Impedance Heating
Impedance systems heat a wide variety of gases, liquids and viscous materials which are stored, pumped and processed in many different industries and applications. Impedance heating can be used in three basic ways:
- Cold Start: Heat is applied to increase fluidity of static, viscous materials so they can be pumped. Typical materials include asphalt, molasses and heavy fuel oils.
- Maintain Temperature or Pipe Tracing: Heat is applied to a liquid or gas flowing through a pipe to offset heat losses. Typical applications include freeze protection or maintaining the fluidity of viscous materials.
- Temperature Rise: Heat is applied to a liquid or gas flowing through a pipe in order to raise its temperature between the inlet and outlet of the heated pipe. Typical applications include heating corrosive liquids or high temperature process air.
Benefits of Impedance Heating
Low Voltage Operation
All systems operate at less than 30 Volts, many at 10 Volts or below. Indeeco systems meet or exceed the requirements of the National Electrical Code (Article 427), assuring safe operation.
Uniform Heating
Because the entire pipe effectively acts as the heating element, heat is generated uniformly throughout its entire length and circumference without hot spots.
Simplicity
The impedance method takes the complexity out of pipeline heating. A few basic components comprise the entire heating system. Installation is simple; it can be installed without disturbing most of the existing thermal insulation.
Wide Temperature Range
Indeeco has pioneered the use of impedance heating for applications ranging from below freezing to 1600o F. It is often the only viable option for high temperature pipeline heating.
Close Control
Thermocouple sensors placed along the pipeline provide precise, uniform temperature control. Optional SCR controls give the ability to achieve control within ± 1o F.
Low Cost
Installation costs are kept to a minimum by the inherent simplicity of the system. Likewise, maintenance is virtually eliminated; many systems operate unattended. Energy costs are low because the required energy is concentrated in the pipe and efficiently heats the fluid or gas traveling through it.
No Burnouts
When the pipe becomes the heating element, burnouts and failures associated with electrical resistance tapes and cables are eliminated.
Advantages Over Conventional Methods
No External Fluids
Pipeline heating with steam or high temperature fluids introduces a high degree of complexity and a potential hazard. Impedance heating accomplishes the same result in a simple, straightforward manner.
No Leaky Jackets
With impedance heating, you won’t have leaky steam lines, cracked steam traps, pump failures or frozen return pipes.
No Hot Spots
Impedance heating eliminates the danger of overheating temperature-sensitive materials (asphalt, chocolate, heavy syrups) because hot spots associated with conventional pipe tracing are eliminated.
No Routine Maintenance
Routine maintenance is eliminated, along with the replacement parts and production shut downs associated with such maintenance.